Reply to dtallon:
You are right there is some similarities to Ag as far as determining location although I'm not as familiar with the details on the Ag side to tell you the exact differences. I do know the construction systems need the GPS antennas to pick up location info from satellites. There's lots or room for error just going off satellites in orbit, so you also need a localized base station located on a surveyed-in control point. The base station sees the same satellites, and since it knows exactly where it is, it can calculate the errors coming from the satellites and send the corrections to the dozer. The 3D design plans have elevation in them, so the system on the tractor uses the GPS to know if it is on, above or below desired elevation. As far as how the blade is actually controlled to design, most GPS dozers use electro-hydraulics, so the system just tells the machine ECM to move the blade up or down to match the design.
Dave
John,
So I actually sell Trimble/Cat Accugrade grade control products for a living, for once on the forum I can provide answers instead of questions haha. How does the dozer automatically control the blade? This may get a little technical so if I confuse you just let me know and I can answer any questions that you may have.
The grade control system is primarily composed of 4/5 major parts. On the dozer blade there are two masts with GPS receivers mounted to the top to accurately know where the blade tips are regardless of blade slope, angle or height, there is a control box or display screen in the cab, and a external radio mounted to the outside of the cab somewhere. On say a new Cat D6T, the dozer is an EH machine, electric over hydraulic so there is an ECM dedicated to the implement. The grade control system connects to this ECM via electrical harnesses and provides inputs and outputs to the blade controls. On older non EH machines we have to tie into the hydraulic valve and add solenoids etc in order for the system to run the hydraulics. Aside from the machine there is an onsite base station mounted on a tripod, and usually a survey rover and data collector. The base station is typically positioned over a know survey pin or survey point, so that the true elevation at that point in the world can be referenced, the rover and data collector are used for checking grades, measuring stock piles, etc.
The base station receives signals from the satellites. The GPS receivers on the dozer also are receiving signal from the satellites. By themselves each of these devices are accurate from about 1 meter to 5 meters (not usually enough in the final grade world), so to tighten the accuracy there is an internal radio in the base station that sends a radio signal to the radio on the cab of the dozer. This radio communication link tightens the accuracy to about 1cm-3cm. (sorry we are in metric up here in Canada)
The engineers of the project build a digital design of the project at hand, which is then uploaded into the display box in the cab. This allows the operator to see the full design of the project, it tells he or she if there are cuts or fills in order to achieve the correct grade as per the design. The operator has different views that can be toggles through of the project, overhead, profile, side view, or a combination of two views. Now the operator has more than just the ability to see the cuts and fills. The operator can push a button that automatically takes control of the blade to insure the highest level of accuracy on the project. There is no auto steer capability in the construction world of GPS yet, that is limited to the agriculture world.
These systems are not just limited to dozers, we have them on graders, excavators, scrapers, packers, pavers, cold planners, skid steers, concrete pavers, drilling machines the list goes on, there are many different applications of how the technology can be utilized for different applications. I have attached some pictures that may help you understand what it all looks like.
Fun fact I have dated automated grade control back as far as 1959 on a Cat motor grader, although there was no GPS is was a system that automatically controlled the blade to maintain a preset blade slope.
As I said feel free to bounce back with any question you may have,
Nathan
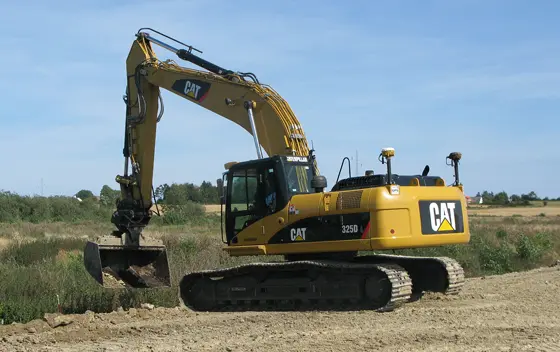



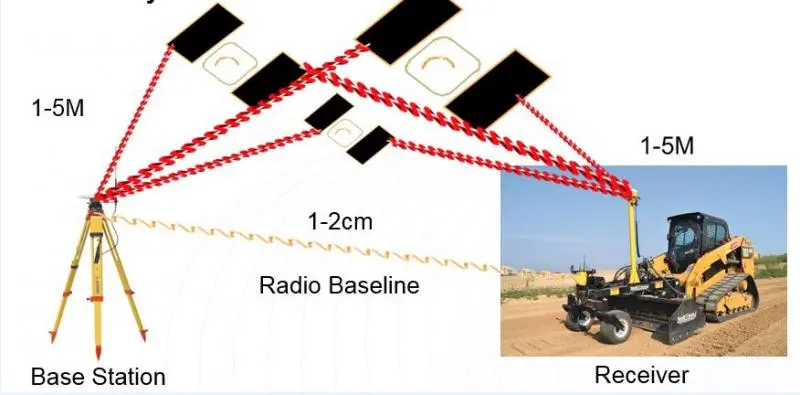
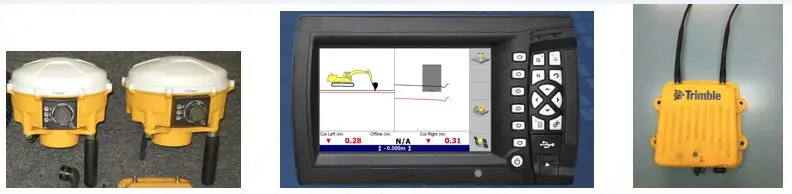
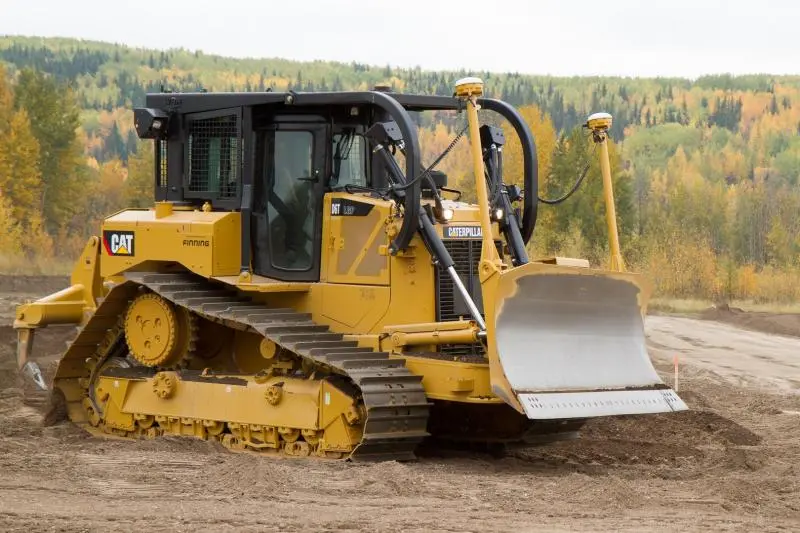