Hi All,
I recently picked up a few old dozers from a fellows son who passed away, a 4G RD4 (seized main, injectors missing), 5J D2 (seems complete, everything turns over) and a D4 7U (seemed ok, missing hydraulic pump but came with a BeeGee). All in non-running condition with unknown history's but I did know none had run since the fellow had owned them and he had them for 15+ years sitting outside. I didn't want them to go to scrap so made an offer for as much as I was comfortable with (way more than scrap) since I knew nothing of their status and we drug them over to our ranch with our backhoe.
[attachment=40639]cats1.jpg[/attachment]
[attachment=40640]cats2.jpg[/attachment]
I decided to start on the 1949 D4 7U and the first thing to repair was the pony motor fuel tank. I've browsed this site and didn't see much info of people using electrolysis for this process and since I've had great luck with it from things as large as engine blocks and as small as motorcycle fuel tanks I figured I'd share the info.
First step was to dump and blow out the tank, it had at LEAST 2 cups of rust chunks and dirt, probably the worst looking fuel tank I've ever encountered. After blowing out the tank I found lots of new holes that were not there before;
[attachment=40641]pony-tank1.jpg[/attachment]
Perfect job for brazing, of which I had never done before. I filled the tank up with as much water as possible and went to filling holes. It took a lot of brazing to get it 100% water tight. The metal was so thin in spots that didn't have holes that water was coming through so the golden glob ended up pretty large and ugly BUT no leaks;
[attachment=40642]pony-tank2.jpg[/attachment]
Pretty ugly inside, this picture makes it look better than it was since some of the water I had already sprayed in loosened and removed some rust right below the fill pipe;
[attachment=40643]pony-tank3.jpg[/attachment]
The magic potion to make electrolysis work is water and some pH Plus (sodium carbonate aka washing soda) from your local stores pool section. I used probably a half cup worth for this, I didn't measure, just dump some in;
[attachment=40644]pony-tank4.jpg[/attachment]
A sacrificial anode (scrap steel) that is insulated from the part you want to de-rust. This anode can not have any metallic contact with your part. This process works line-of-sight so you might have to get creative on some types of parts;
[attachment=40645]pony-tank5.jpg[/attachment]
[attachment=40646]pony-tank6.jpg[/attachment]
Then you connect a cheap trickle style 12v battery charger (not a fancy auto-sensing type) or find an old low amp DC power supply and put some gator clips on like I have. This one here has an output of 12V DC and 1 AMP. Positive to the anode and negative to your part;
[attachment=40647]pony-tank8.jpg[/attachment]
Let the magic begin;
[attachment=40648]pony-tank7.jpg[/attachment]
After a day or so, disconnect the power, remove the anode, clean it up with a wire brush and put back in and hook it up again. I do this over several days until the anode is no longer collecting any appreciable metal. I try to put the anode back in at different angles to increase the chance of getting all the nooks and cranny's;
I then drain the tank, rinse it out good, toss in a handful of nuts to swish around a little while to knock off anything else that might be left behind then blow it out with compressed air;
[attachment=40649]pony-tank10.jpg[/attachment]
At this point you could put in a little diesel or 2-stroke fuel to stir around and coat the inside to keep from flash rusting before re-installing.
I decided to go a step farther and coat mine with POR-15 Tank Sealer, $15 will get you an 8 oz can which is enough to do an automotive sized tank. You can either purchase the prep kit from POR-15 or do what I did and get a jug of "Klean-Strip Phosphoric Prep and Etch" from the big orange box store for $15 (be safe, read instructions, use gloves, face shield, etc). I put in about half a tank full at full strength and occasionally swished it around to keep it all wet inside for around 30 minutes. After this, drain the acid back to it's original container, flush the tank with water until it comes out clean then poor in a couple cups of Acetone and swish all around to absorb the rest of the water.
The Phosphoric acid will leave a little zinc coating to help prevent flash rusting. This would also be a good thing to do even if you weren't going to coat it, it will help protect the surface for awhile.
After the Acetone I set the tank up and let a little fan blow in the filler neck for an hour or two just to make sure it's good and dry before doing the tank sealer.
For the POR-15 I just followed the instructions, poured it all in, rotated the tank around slowly making sure all surfaces got coated then drained for an hour. You don't want this stuff to puddle so I angled the tank so everything drained to the drain plug for that hour. After that, let the tank dry for a few days before putting any gas in it. The POR-15 container usually gets ruined just taking the lid off so I put mine back in a glass jar in hopes of using for the D2 tank later.
I also rebuilt the carb during the same time, I found lots of good info here about this process so I won't go in to any detail other than I did make all my own gaskets from Felpro gasket sheets. The kit online for this Zenith carb is like $60 and I didn't need any other parts so I saved myself some money there;
Top gaskets are old, bottom are homemade;
[attachment=40650]carb-gaskets.jpg[/attachment]
Re-assembled;
[attachment=40651]D4-carb1.jpg[/attachment]
Installed;
[attachment=40652]D4-carb2.jpg[/attachment]
And the payoff;
[video]https://youtu.be/2UmqK3X_eow[/video]
The pony started on the first pull! The main ended up needing the old diesel drained and the fuel system primed before it would fire but with fresh fuel it came right to life. Still lots left to do, only shifts in to 1st and reverse but clutches and brakes are good.
Thanks,
Jordan
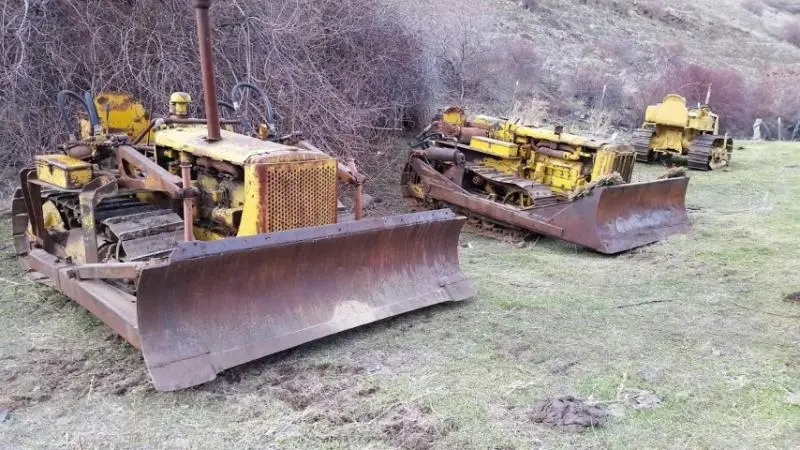
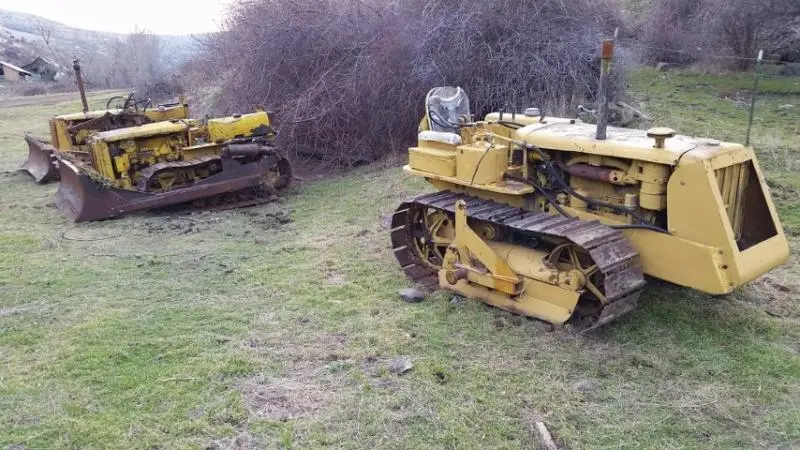
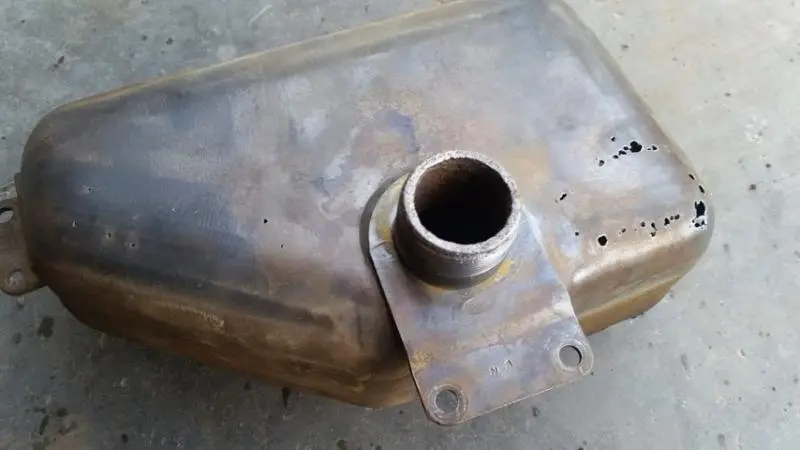
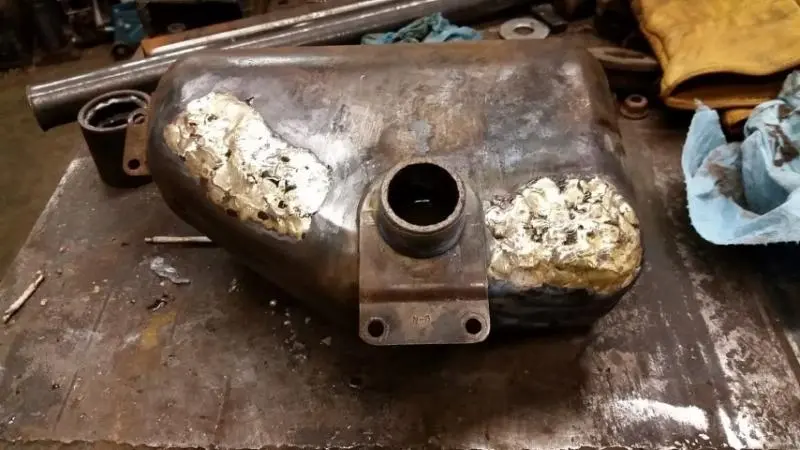
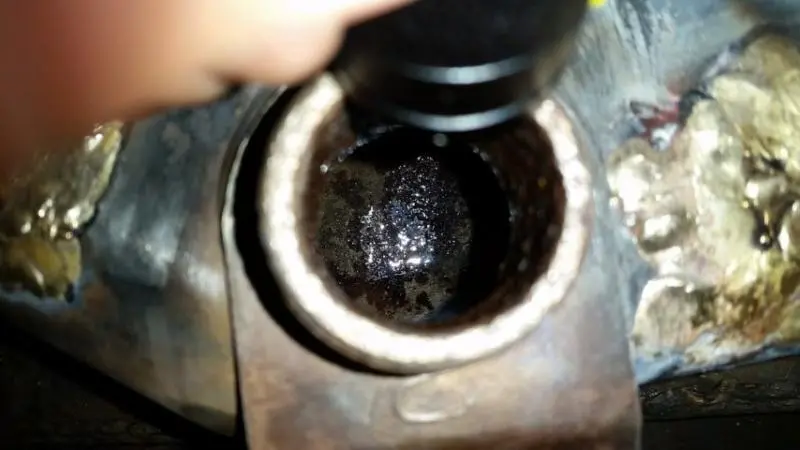
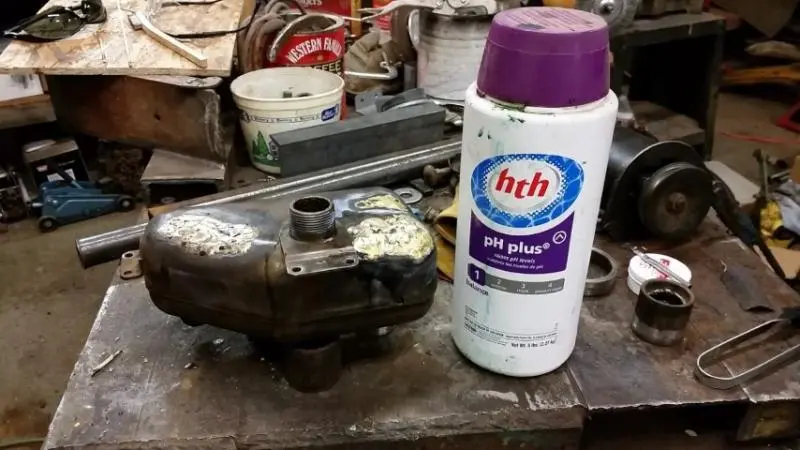
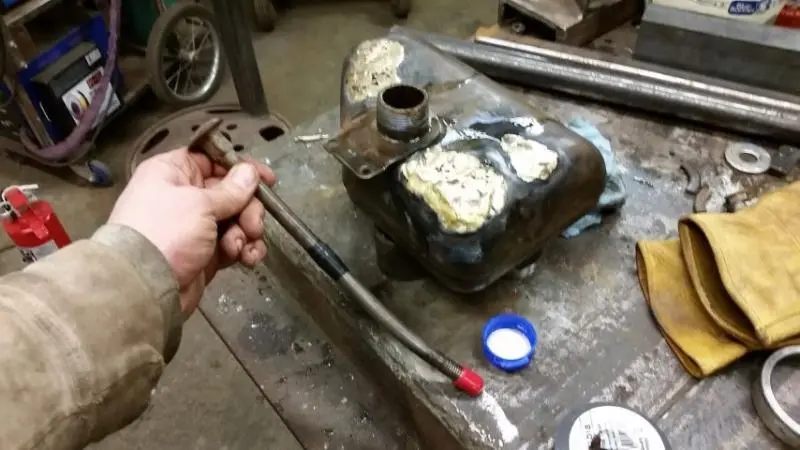
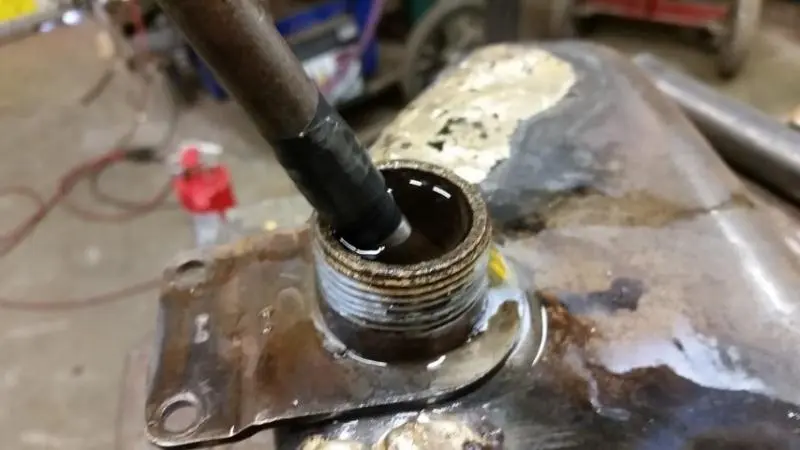
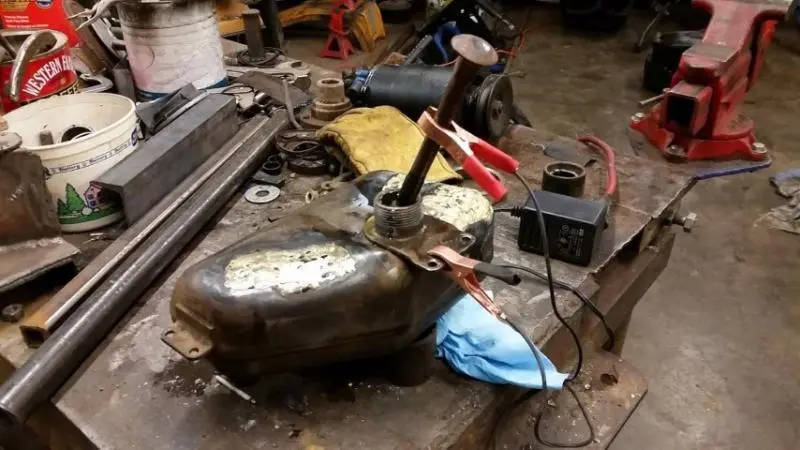
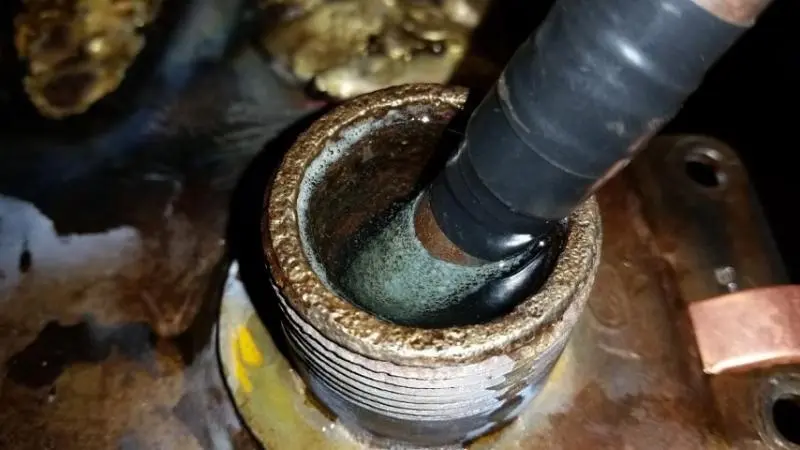
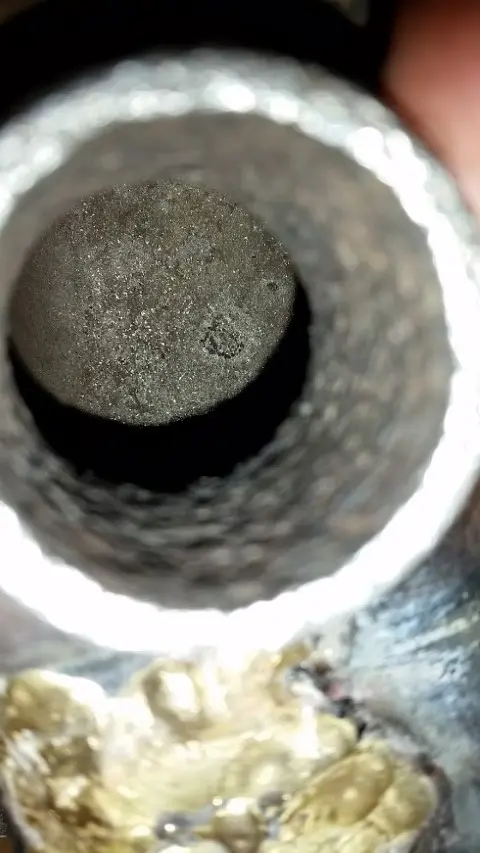
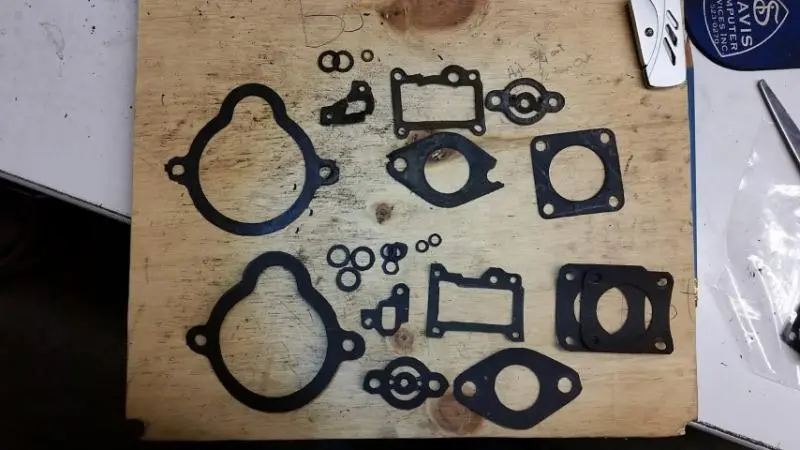
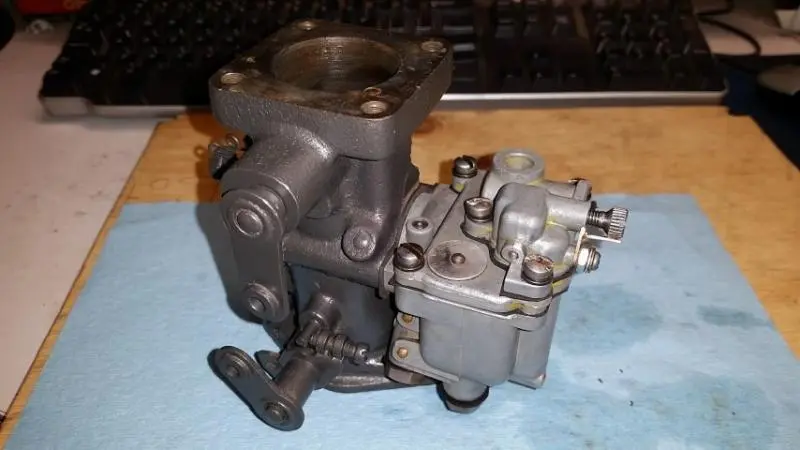