I'm in the middle of rebuilding three D6 size pony engines right now. The first two blocks are cleaned up and ready for boring. The third one was pretty rusty so at first I thought it would be a parts donor. I pulled off the cylinder heads yesterday to see how "stuck" everything would be. As usual, one bore is nice and the other is rusty. This is because the engine will stop coming up on compression on one side, while the other side has open valves and that's where they get rusty.
So on this rusty engine, I found standard cylinder bores, which was surprising. The flywheel nut didn't have the cold chisel marks as most do and the intake manifold didn't seem like it had ever been off. I'm thinking that this is an unmolested pony and may have potential. When I get the manifold off, I notice that one lifter is stuck way off the cam... Odd. Then I look at the valve box for that side and look what I found (first picture). I've been a bit curious about these clips holding the valve guides in place. The counterbore that they sit in isn't really deep enough to really retain the clips well. Notice that the second valve had a clip that was falling out and the clip for the opposite side is below the spring. There is no way that someone took this apart and left it that way as the manifold gasket was stuck in place and bolted down. I bet this thing really made noise as it was dying. Has anybody seen a pony fail in this manner? I'd suggest anyone rebuilding one make sure that the clips are bent so that they clamp the guide snug and that they seat well in the counterbore in the block.
So, now I'm curious as to whether these loose valve guide clips were installed this way from the factory. I had not seen anything that indicated that it had been apart before. Next, I had to get the flywheel off. WOW, this one was stuck. I had a piece of heavy angle iron with two holes for the pulling 3/8"-16 bolts that worked perfect for the previous two engines. This one would not budge. Next, I drilled a 1" thick bar and started tightening. Added LOTS of MAPP gas heat. Heated, cooled, heated cooled, left overnight with pressure, no budging. OK, next. I decided to turn down the air pressure on my impact wrench and hammer a bit on the puller bolts- snap, the 3/8" grade 5 bolt snapped. Next, add a grade 8. Snap.
In the process, I decided to try something I know a lot of you have done lots of times. No idea why I've never tried it on stuck bolts as I've had a Miller wire feed in my shop for 20 years or more. I welded a nut to the broken stud in the flywheel and it came out incredibly easy. I'll definitely be trying this again on a broken bolt that is rusted in tight sometime.
So, I still could not budge the flywheel. Finally, I took a really big C-Clamp. I put it over the flywheel and rested the outside of the clamp against a strong area of the cylinder block (between the back of the flywheel and block). Then I heated the hub again and gave the bar a sharp whack with a hammer and it popped loose. I know you don't want to whack the crankshaft and break the pins in the bearings. With the clamp, the flywheel couldn't move toward the block. If the pistons weren't stuck, I could probably have pulled the crank and flywheel out and pressed the flywheel off the crank. I couldn't get to the stuck rod nuts.
The final surprise on this was that somebody had been inside before. The crankshaft had been ground .020/.020. I've disassembled a lot of engines in my years, but have never seen a standard bore engine with a re-ground crankshaft. I guess that whoever re-did the crank installed the valve clips.
Sorry for the long winded description, but some of it might help others- or at least to really watch the valve guide clips when reassembling your pony.
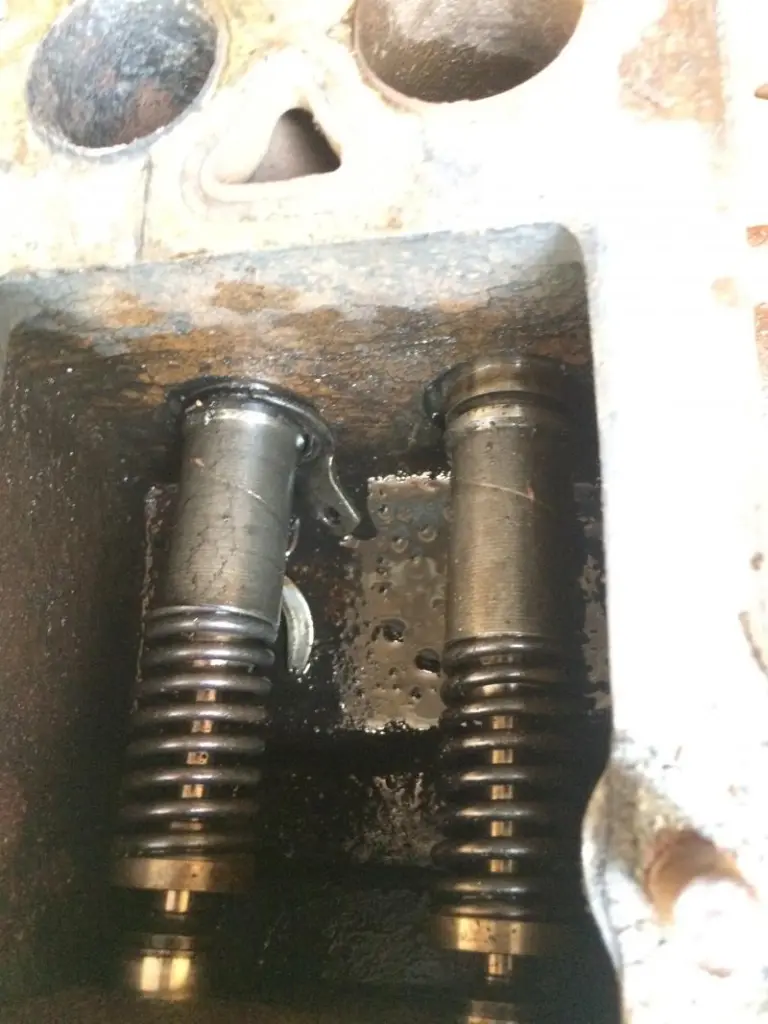
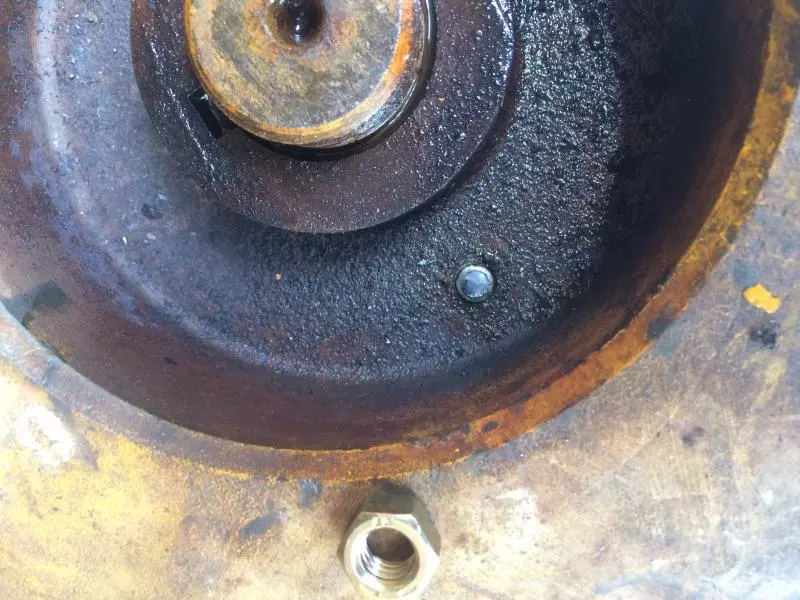
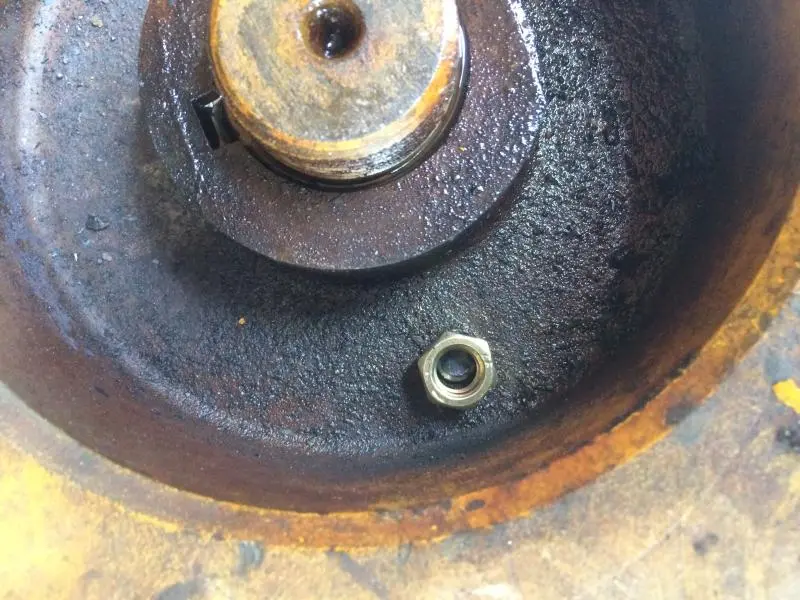
