Reply to STEPHEN:
For the bearing that controls the end play, I haven't seen any that were worn 3/16, my best guess is that the dowel is loose. If keeping the rods centered in the piston is of any concern, as well as the output gear and bearing oil
hole alignment, I would repair the loose bearing.
Hi Team,
if you went the turn the bearing route you will need to re-drill the 2 crank journal lube holes either side of the dowel pin or the bearing will starve of oil and likely seize up.
If it is a loose dowel then you may still be in trouble as it is the length of the bearing that sets the end float between the crank side face and the output drive gear--new gears should come over length and are then machined as needed to achieve correct end float.
If your outer bearing is good it can happen that someone has driven on the end of the crank to loosen the flywheel from its taper and broken a piece out of the bearing support area that contains the flimsy dowel--most often it is this abuse that loosens the bearing and dowel--A puller should be used and thought given to transferring any shock given to the sides of the cylinder block with wooden spacers of adequate area to spread the load and not cause cracking of the water jackets.
be aware these cranks have been known to break thru their centre web after being abused by hitting off/on the flywheel.
Flywheel Nut tension is 150 to 165 lbs/ft and all care should be taken to not cause bending in the crank when working with the nut doing up or undoing--support under the flywheel to the flywheel cover.
OM has a u-beaut tool he made up for doing this without putting excess stress on the crank.
Some time back some one posted a very good run down on putting thrust washers each side of the crank.
Scans below outline some of this.
Some have found main bearings to be un-available in the undersize, or even standard maybe, so have machined bronze bearings and put white metal liners in them or someone posted the specification for alloy bearing material that is very like Toyota piston alloy. melt down some Toyota pistons and cast suitable stock to machine into bearings--more than one way to skin a Cat.
Cheers,
Eddie B.
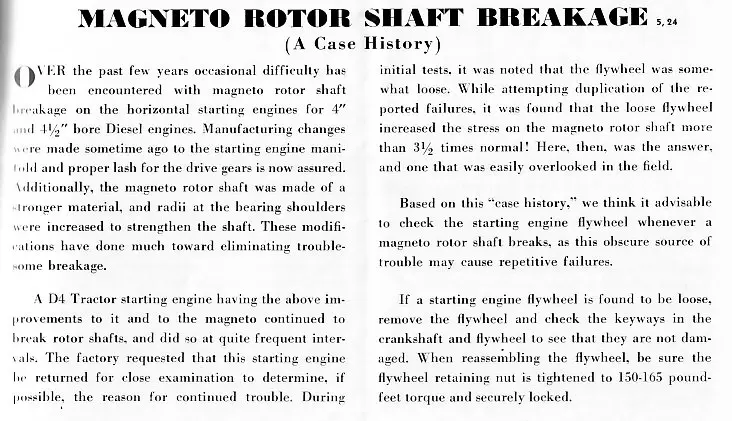
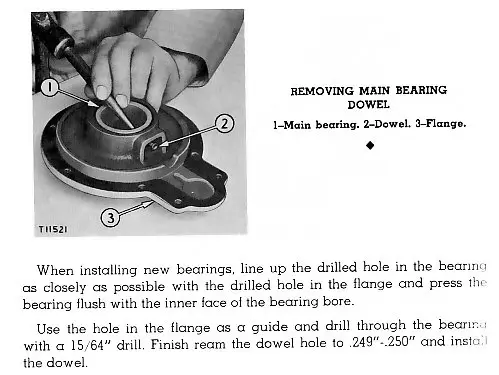