2TonIron - None of the tool guides give any dimensions for the spacer nor the puller arm (also called a puller leg).
You will have to get someone who owns a puller arm to measure the hole spacing, and someone who owns a spacer to do the the same.
The 5F9040 number is actually a group, comprising the leg, the pin, and the adaptor with the eyes for the pin. The actual leg P/N is 5F9306. It is a common leg, and still a current part, AFAIK.
5F7334 spacer actually consists of 3 components, none of which are listed separately, and they're all obsolete.
There are two spacers, P/N 5F7690 and 5F7693, one of which fits over the other. Then there is a plug, P/N 5F7694, which fits into the topmost spacer, and which takes the pressure of the hydraulic press head.
I'll try a few pics. The first is a pic of the spacer, itemised as "P".
The second pic is the sprocket pulling setup. Sorry about the poor quality, the old pics in these old books don't scan well.
[attachment=26292]Cat tools.jpg[/attachment]
[attachment=26293]Sprocket puller.jpg[/attachment]
Your idea of the plates behind the sprocket will work just fine. Make sure the materials you use are high strength steel (T1 equivalent).
Those presses really lay on the pressure and you don't want weak parts failing and turning into missiles in your shop.
You will also probably need to whack the sprocket with a sledgehammer to make it let go, once you have substantial pressure on the press.
Don't forget to just loosen the sprocket retaining nut and leave about 1/4" gap between nut face and sprocket face to allow the sprocket to pop off, without it flying right off the shaft and across the floor!
The 5F7334 spacer sits against the end of the sprocket driving hub and clear of the sprocket shaft (the dead axle).
The pressure has to be applied to the end of the sprocket hub without any pressure on the dead axle.
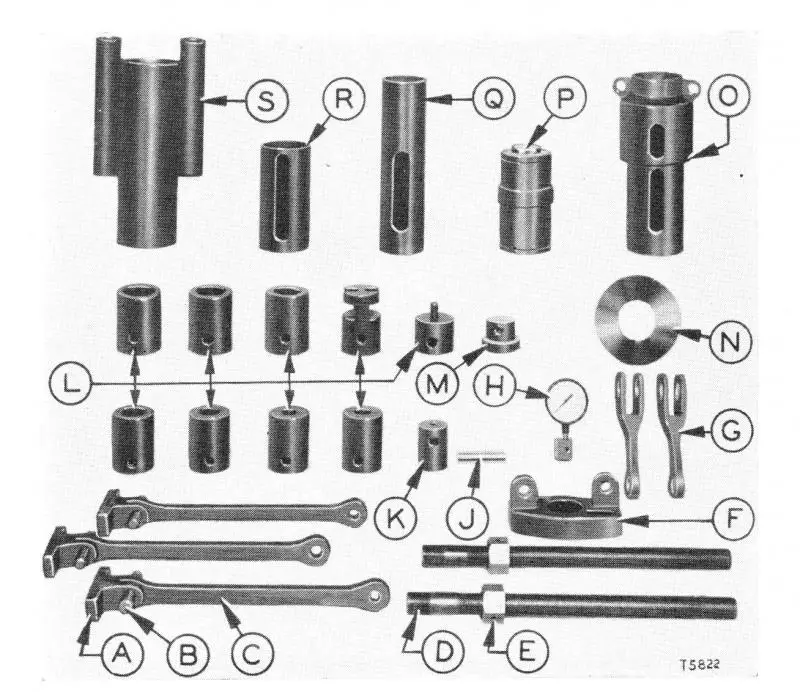