I have had an old WWII military winch in storage for quite a while and I have had a pipe dream to design a well thought out mount to get it back on a machine. It used to be on my narrow gauge 22 with a cobbled up frame made by the previous owner. This mount had the seat raised up to sit on top of the fenders to provide room for the clutch control and framing. We used it for light logging for many years but when I restored that cat, I took it off as it did not live up to the like new and stock condition of the restoration. Long story short, I have spent a good deal of time and thought into a more professional style that should work out just fine. Power to the winch is from the stock PTO. I will install it on my wide gauge "daily driver" 22.
Some before pictures to kick it off. The nicest thing of the old mount was the incoroporation of the logging sheave. This worked very good as a substitue to a normal fairlead and in combination as a mini arch. I opted not to use the sheave in order to simplify the frame design, and not have such a high placed vertial load sticking out so far from the back of the tractor. I will not use this for logging so the extra height, although minimal is not needed.
[attachment=38334]winch.jpg[/attachment][attachment=38335]IMG_1076.jpg[/attachment][attachment=38336]IMG_1077.jpg[/attachment][attachment=38337]IMG_1078.jpg[/attachment]
The winch itself is a Heil brand, model 125-G I believe, 10,000 or 12,000 pound unit. Almost identical and interchangeable to the very popular Garwood brand used on 6x6 military trucks. Since these pics were taken, I have dismantled the unit for a complete clean and inspection. It is sandblasted and will be painted up nice. Gears were good. I know it is powerful enough to snap a 5/8" cable, which I have witnessed (caused!).
I am a mechanical engineer by profession and I have CAD software to make the model and subsequent drawings. I love doing this where I reverse engineer not only the winch but the tractor mounting points and other constraints, and then design from there. My requirements were this:
1. Must fit in the space under the seat in the original position.
2. Must be able to utilize the orginal draw bar including the swing capability.
3. Controls design and placement require little to no modification to the original fenders, etc. (no big holes).
4. Must not protrude any farther than necessary from the back of the machine. The mounting pattern for the original draw bar support is not strong enough for a long cantelever shape. You can barely see in the pictures I have added additional mounting bolts that will connect to a shear plate mounted to the final drive case (plate not shown yet).
5. Need some provision for side pulls either by fairlead rollers or the sheave method. I ended up going with fairlead rollers.
I am happy to say that I have been successful, so far.
I have attached two shots of the model. The cat is of course yellow, and the winch is green. The new steel frame is gray. The drum release clutch control is blue, which comes out at the right side of the seat box. Details not shown are the brake cable and lever. For the brake lever, I am using a Honda Civic emergency brake handle. More pics on that later. I actually made two designs, which used different approaches for winch assembly in the frame. The first was a wrap around box with the winch coming out from the top. I then made the current and final design which allows the winch to be removed out the back of the frame. This is why the back plate is removable, the all the guts come out straight back. The frame can stay mounted to the tractor this way too. The only clearance issue I see is that I have to use a low profile hitch pin for the draw bar if I let it swing. It gets tight on the left and right swing side, but the drawbar can swing fully.
[attachment=38338]Winch on cat2.jpg[/attachment][attachment=38339]Winch on cat3.jpg[/attachment]
The plate parts are ordered from the laser cutter right now. Total price is about $350. Not cheap but worth it to me. Rollers cost $120. I am looking forward to getting the parts here and starting the welding assembly. I will of course post progress pictures as I go.
Enjoy!
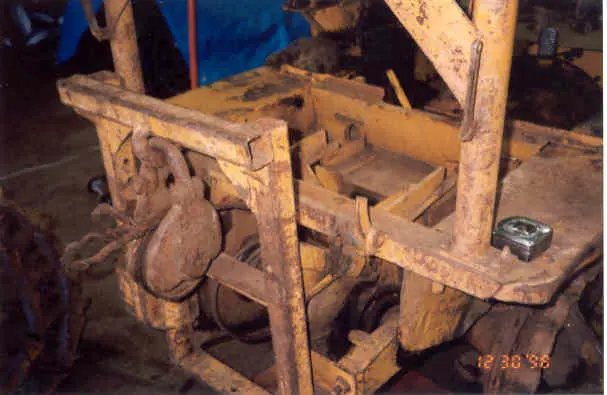
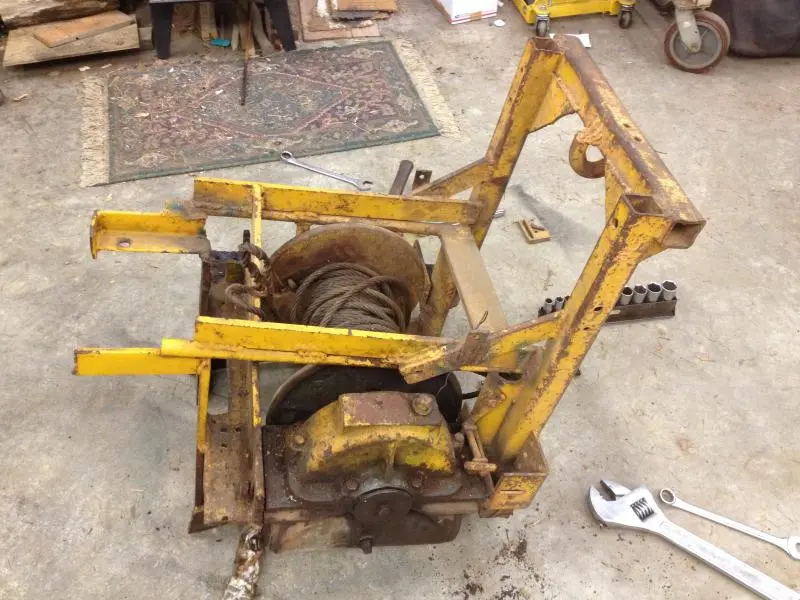

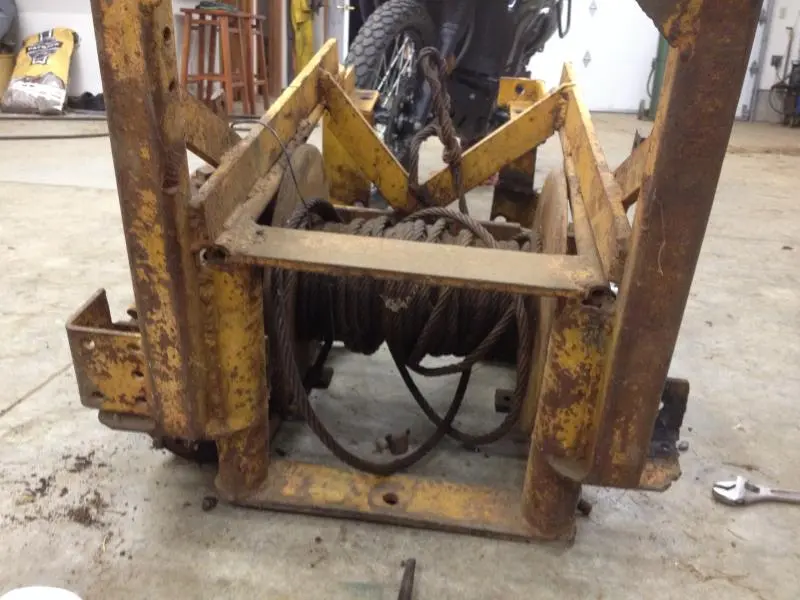
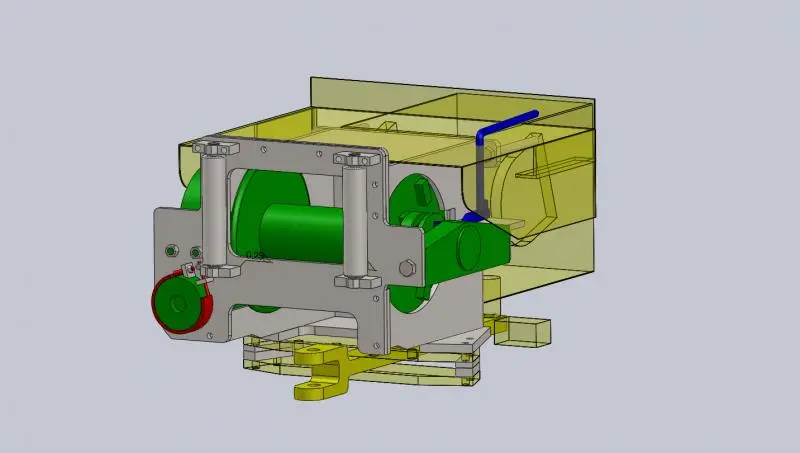