Reply to reclineaholic:
[quote="n7gxz"]Question for you, how are you going to work the ground? Are you setting up a slip ring? You don't want to flow the ground through the headstock bearings.
Kevin[/quote]
Good point, I hadn't really thought about that but I definetly don't want the ground going thru any bearings... It's not going to turn very fast, one revolution in 4 to 5 minutes, and the duty cycle on my welder is probably going to require me to stop for a couple minutes after each revolution... Maybe just let the ground wind around the tail stock one time and then fix it while the welder is cooling?
Sent an email to Lincoln this morning to find out what wire they suggested for this job, got an automated answer a few minutes later, it said they would have a tech try to answer my question within two days. Well I'm not very patient so I called their main office and asked if there was someone who could help me pick a mig wire for a specific application, they connected me to a tech that suggested Lincore 55-G as long as I didn't go over 3/4" thick so I ordered some from weldingsupplies.com...... Just checked my email, and there was one from a Lincoln applications engineer and he said to use Lincore 33 ?? So much for a final answer.
Guess I'm gonna stay with the Lincore 55-G unless someone tells me they tried it and it didn't work.
hi reclineaholic, you may want to invest in making a waterbath and a set of rollers so that you can build up the rollers without the need to
fully dissasemble them.
i used a lincoln 400 amp to do the job and just standard MS copper coated wire. yes i am sure its not ideal but i was at the end of my tether with money and figured well bugger it, I'll give it a go.
i have done about 40 hours now and cannot see the slightest bit of wear on the rollers.
ditto on welding in the lathe, though you would be able to make up a set of polyethylene soft jaws to grip the roller and effectively isolate the roller from the chuck if you wanted to.
i made a jig that would spin the roller at a constant speed while being in a water bath out of bits and pieces round the house. if you have a lathe you would be able to do the same.
my guess would be that the best rpms were about 0.7-.9 rpm for a roller that is approximately 200mm in diameter.
for earthing, i used a 15 dollar magnetic earth clamp, with a c shaped bracket i would tack welded to each roller to allow for a flat surface. worked well.
i used a windscreen wiper motor to drive one roller while the other was simply a free spinning roller.
the best beads were laid with the roller rotating away from the gun, with the gun pointing uphill, and zig zagging about a 15mm wide bead along the length of the roller. i canpretty much guaruntee you are going to be working at at least 200 amps as you need the heat to evaporate the water off otherwise the weld will sputter. i am pretty sure i was welding at around the 270-300 amp range
took a bit of learning to work out the best way, so be ready for a couple of days welding. holding the welder still and doing single line beads was pretty messy in the end, but give it a go and see what works best for you.
as with everything,theres always more then one right way.
hope this helps. : )
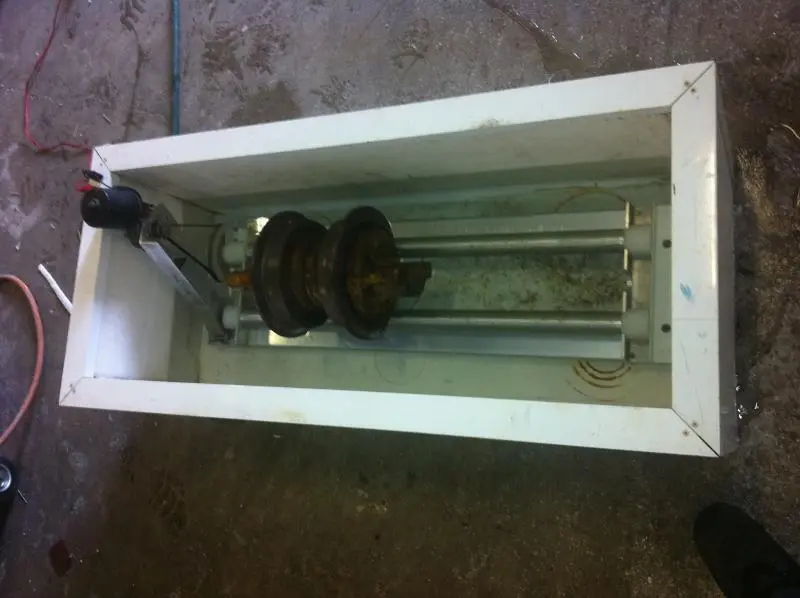